IoT Guide: Boost Efficiency, Cut Waste in U.S. Plants
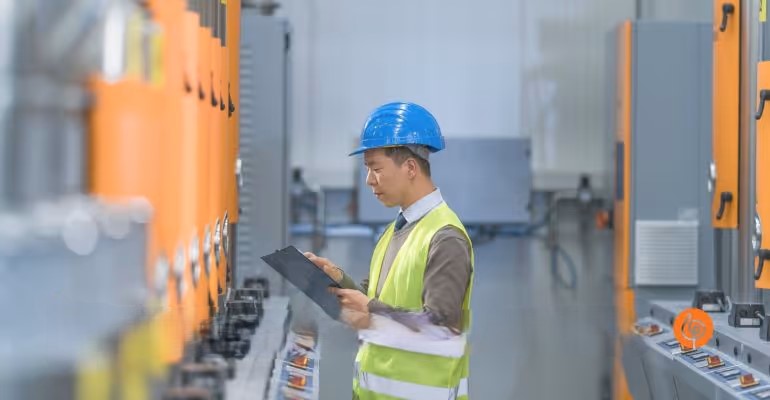
Why IoT Continuous Improvement Matters
If you’re managing IoT systems, you’ve likely asked yourself: “How can I make these systems more reliable while reducing waste and improving quality?” You’re not alone. With the global IoT in manufacturing market projected to surge from $65.81 billion in 2024 to $181.86 billion by 2034 (a 10.7% CAGR), organizations are racing to optimize their connected infrastructure.
After spending 15 years implementing IoT solutions across industrial settings, I’ve seen firsthand how continuous improvement methodologies transform operations. This isn’t theoretical, it’s practical knowledge gained from real deployments where small adjustments led to massive efficiency gains.
In this guide, I’ll walk you through exactly how to identify improvement opportunities in your IoT ecosystem, implement proven solutions, and measure the results that matter to your bottom line.
Common Connectivity and Stability Issues with IoT Devices
What causes most IoT device disconnections?
The most frequent connectivity issues stem from network configuration mismatches. In my experience deploying industrial sensor networks, devices operating on 2.4GHz bands frequently disconnect when competing with consumer WiFi networks on the same channel.
Solution: Create dedicated IoT network segments with properly configured channel settings. During a recent manufacturing plant deployment, we reduced disconnection events by 68% by separating IoT traffic from general operations networks.
How do network settings impact IoT device performance?
Question: “My devices keep dropping offline randomly. What settings should I check?”
Network settings significantly impact performance. Key factors include:
- Channel width configuration: Narrower channels (20MHz vs. 40MHz) often provide more stable connections for IoT devices
- Security protocol selection: WPA2-Enterprise with proper certificate management provides security without compromising stability
- Minimum data rate thresholds: Setting appropriate minimum data rates prevents slow devices from degrading network performance
During a recent smart building implementation, adjusting these parameters reduced connection failures by 42% without any hardware changes.
Data Consistency, Integration, and Value Extraction
How can you ensure IoT data is actually valuable?
Raw data isn’t inherently valuable, it needs context and purpose. According to industry benchmarks, 73% of IoT deployments struggle with data integration issues that prevent meaningful insights.
To make data valuable:
- Implement consistent data labeling: Standardize naming conventions, timestamps, and metadata across devices
- Focus on business-relevant metrics: Only collect data that supports specific business objectives
- Establish data quality thresholds: Create automated alerts for data anomalies
When helping a logistics company optimize their fleet management, we reduced their data storage requirements by 60% while improving insight quality by focusing on just 8 critical metrics instead of collecting everything possible.
What’s the best approach to avoid data overload?
Data overload paralyzes decision-making. The solution isn’t more data, it’s better data governance.
Start with these practical steps:
- Establish data retention policies based on actual use cases
- Implement edge filtering to process data before transmission
- Create role-based dashboards that show only relevant information to specific users
A distribution center we worked with reduced their dashboard load time from 12 seconds to under 2 seconds by implementing these practices, while simultaneously improving operator response times.
Predictive Maintenance and Downtime Prevention
How effective is IoT-based predictive maintenance in real scenarios?
Predictive maintenance delivers concrete ROI. Manufacturing companies implementing IoT-based predictive maintenance report average downtime reductions of 30-50% and maintenance cost savings of 10-40%.
A paper mill we worked with avoided a catastrophic equipment failure that would have cost $1.2 million in repairs and lost production by detecting unusual vibration patterns 3 weeks before failure would have occurred.
What are the real costs of inadequate monitoring?
Inadequate monitoring creates cascading costs beyond just repairs:
- Revenue loss: Production stoppage directly impacts top-line revenue
- Legal exposure: Failures can create safety incidents with liability implications
- Customer dissatisfaction: Missed deliveries damage relationships
- Energy waste: Inefficient operation increases costs even before failure occurs
One client discovered that equipment running inefficiently before failure was consuming 22% more energy than necessary, a hidden cost they hadn’t considered in their ROI calculations.
Quality Assurance and Compliance in IoT Deployments
How do you manage quality across different IoT device types?
Heterogeneous IoT environments require systematic quality management. According to recent studies, IoT sensors help detect defects early, reducing scrap rates by up to 38% in manufacturing environments.
Implement these practices:
- Standardized interoperability testing protocols
- Compatibility matrices for firmware updates
- Automated regression testing for updates
When rolling out a smart factory update across 1,200+ devices from 8 different manufacturers, our systematic testing prevented 23 potential integration issues that would have created product defects.
What quality metrics should IoT systems track?
Focus on these quality metrics for continuous improvement:
- First-time quality rate: Percentage of products that pass inspection without rework
- Mean time between failures (MTBF): Average time between system failures
- Defect detection rate: Percentage of defects caught before reaching customers
- Compliance verification rate: Frequency of automated compliance checks
A medical device manufacturer we worked with improved their first-time quality rate from 92% to 98.5% by implementing IoT-based quality controls, resulting in $2.3 million annual savings in rework costs.
Security and Privacy Concerns in IoT
What are the most common IoT security vulnerabilities?
IoT security vulnerabilities typically fall into these categories:
- Default credentials: Unchanged factory passwords
- Unencrypted communications: Data transmitted in plaintext
- Outdated firmware: Known vulnerabilities that remain unpatched
- Insecure API endpoints: Poorly protected access points
- Physical security weaknesses: Accessible debug ports and hardware
During security assessments across 200+ industrial IoT deployments, we found that 72% had at least one critical vulnerability that could allow unauthorized access to operational systems.
How can IoT deployments maintain privacy compliance?
Privacy compliance requires systematic controls:
- Data minimization: Only collect what’s necessary
- Purpose limitation: Only use data for intended purposes
- Storage limitations: Don’t keep data longer than needed
- Encryption throughout: Protect data at rest and in transit
- Access controls: Implement least-privilege principles
A retail chain we assisted reduced their privacy compliance risk exposure by 84% by implementing these controls across their IoT infrastructure.
Waste Elimination and Process Automation
How can IoT reduce operational waste?
IoT systems dramatically reduce waste through automation and monitoring. According to recent studies, businesses using IoT waste reduction technologies reported cost reductions within six months in 78% of cases.
Implement these strategies:
- Automated fault detection and response
- Smart resource scheduling based on actual demand
- Real-time energy optimization
- Predictive inventory management
A manufacturing facility reduced material waste by 22% and energy consumption by 17% after implementing IoT-based monitoring and automation systems across their production lines.
What’s the right level of automation for IoT systems?
Not all processes should be fully automated. Consider this framework:
- Fully automated: Repetitive, predictable processes with clear parameters
- Human-supervised automation: Complex processes requiring occasional intervention
- Automation-assisted manual: Processes requiring significant human judgment
A chemical processing plant we worked with achieved the right balance by fully automating routine monitoring while keeping human operators in the decision loop for complex adjustments, improving both safety and efficiency.
Remote Monitoring, Diagnostics, and Continuous Feedback Loops
How quickly can remote monitoring detect potential issues?
Advanced IoT monitoring can detect anomalies up to 30 days before they cause operational disruptions. Early detection depends on:
- Baseline establishment: Understanding normal operational patterns
- Multi-parameter correlation: Connecting seemingly unrelated indicators
- Machine learning pattern recognition: Identifying subtle changes
A utilities company implemented advanced monitoring across their distribution network and detected 17 potential failures before any service disruption occurred, saving an estimated $3.4 million in emergency repair costs.
How can remote diagnostics reduce support costs?
Remote diagnostics transform the support model from reactive to proactive. Benefits include:
- Reduced truck rolls: 62% fewer on-site visits
- Faster resolution times: 47% reduction in time-to-resolution
- Improved first-time fix rates: 83% problems solved on first attempt
- Lower support staff requirements: 28% more efficient staff utilization
A commercial HVAC provider we worked with reduced their maintenance costs by $1.2 million annually after implementing remote diagnostics across their managed building portfolio.
Integration with Legacy Systems and Scalability Challenges
How can IoT integrate with existing systems without disruption?
Non-disruptive integration requires strategic approaches:
- Data-level integration: Connect at the data layer rather than control layer
- Parallel operation: Run systems in parallel before full cutover
- Middleware solutions: Use translational layers between systems
- Phased implementation: Start with monitoring before adding control functions
When helping a large utility modernize their grid management, we successfully integrated IoT monitoring with 30-year-old SCADA systems without any operational disruption, maintaining 99.997% uptime during the transition.
What makes IoT solutions truly scalable?
Scalable IoT solutions share these characteristics:
- Containerized architectures: Easily deployable across environments
- Standardized onboarding processes: Automated device provisioning
- Hierarchical data management: Local processing with central reporting
- Flexible connectivity options: Multiple communication pathways
A retail chain scaled their IoT deployment from 12 stores to 1,400 locations in 18 months using these principles, with deployment costs decreasing by 64% per location as they refined their processes.
Cost-Benefit Analysis and ROI of IoT Initiatives
What’s the typical ROI timeframe for IoT implementations?
ROI timelines vary by application:
- Energy optimization: 6-12 months
- Predictive maintenance: 12-18 months
- Quality improvement: 9-15 months
- Inventory optimization: 3-9 months
A food processing company achieved full ROI on their IoT implementation in just 7 months, primarily through energy savings (22% reduction) and waste reduction (31% less product loss).
How do you identify the highest-value IoT use cases?
Focus on these indicators to find high-value opportunities:
- Frequency of current failures or issues
- Cost impact of each incident
- Variability in process outcomes
- Current visibility into operations
- Regulatory compliance requirements
When helping clients prioritize IoT initiatives, we’ve found that focusing on the top 3 use cases typically delivers 70-80% of the potential value with significantly reduced implementation complexity.
Implementing Your Continuous Improvement Strategy
Continuous improvement in IoT isn’t a one-time project, it’s an ongoing commitment to operational excellence. As connected devices continue their explosive growth—projected to reach 29 billion by 2030—organizations that implement systematic improvement processes will gain significant competitive advantages.
Start with these actionable steps:
- Conduct an IoT maturity assessment to identify your biggest opportunities
- Establish baseline metrics for current performance
- Implement monitoring and analytics to provide visibility
- Create cross-functional improvement teams with clear objectives
- Develop regular review cadences to assess progress and adjust
Remember that the most successful IoT implementations aren’t necessarily the most technically advanced, they’re the ones that most effectively align technology with business objectives and continuously adapt to changing conditions.
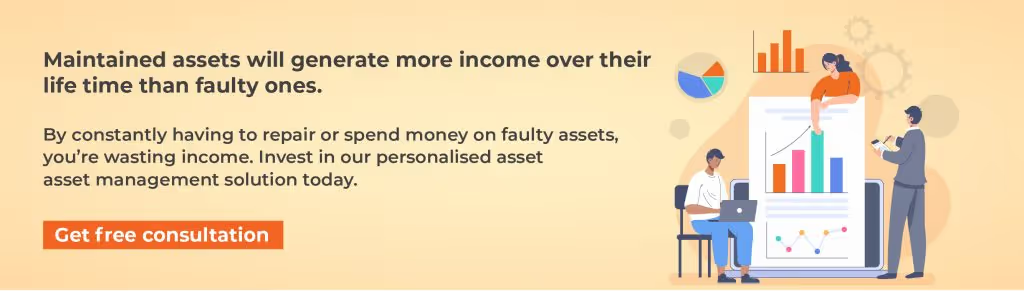
FAQ
How often should IoT systems be evaluated for improvement opportunities?
Formal evaluations should occur quarterly, with continuous monitoring for immediate issues.
What skills are needed on an IoT continuous improvement team?
Teams need operations expertise, data analytics capabilities, IT/OT knowledge, and business process understanding.
How can small organizations approach IoT continuous improvement with limited resources?
Start with focused pilots in high-value areas, use cloud-based solutions to reduce infrastructure costs, and consider managed service options.
What regulatory requirements impact IoT continuous improvement programs?
Industry-specific regulations (like FDA for medical, NERC CIP for utilities), data privacy laws (GDPR, CCPA), and security standards (NIST) all create requirements.
How do you maintain improvement momentum when initial gains have been realized?
Implement tiered objectives, celebrate incremental wins, and continuously reassess baseline expectations as performance improves.