Digital Maturity: The backbone of advanced smart manufacturing
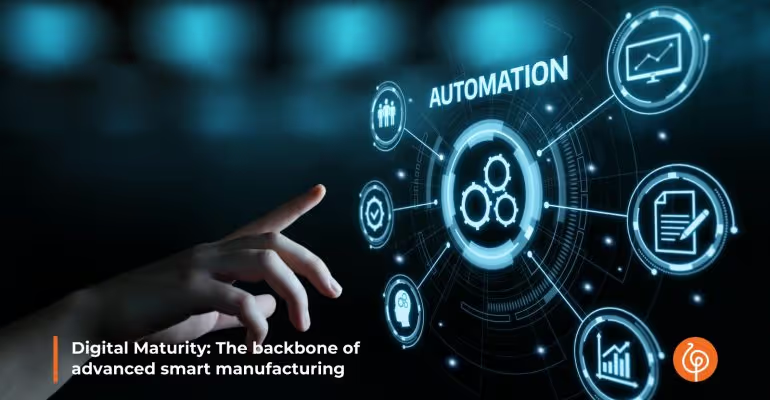
The six pillars of digital maturity
1. Clear-cut goals and objectives
Digitally mature manufacturers focus on specific performance deliverables as opposed to random technological exploration. Before adopting a particular technology, they establish very specific improvement or innovation goals.
Knowing why the organization is pursuing digitization, and highlighting the anticipated gains, sets the foundation for successful digital transformation.
To read more: Manufacturing Shop Floor Job card digitization
2. High-performing workforce
Smart factories need smart skills. Talent issues have haunted manufacturers for quite some time now. It is highly crucial for manufacturers to close the skills gap between the expertise required to transform the enterprise and the current lack of digital skills.
Organizations should also create a culture of collaboration, facilitate advanced analytics to drive better business decisions, and foster a healthy growth mindset oriented towards constant learning to achieve digital maturity.
3. Data-driven business decisions
Integrated digital networks collect data across the enterprise and process it to identify and address opportunities for process improvements.
Although machine data collection dates back to the invention of Programmable Logic Controller (PLC) in 1969 by Dick Morley, modern industrial IoT platforms completely reinvent the game of data collection. They can ingest data from hundreds of different machines or sensors, and use it to streamline business processes.
This data is related to the manufacturing assets, and typically includes, operational data, asset health, performance, usage, maintenance, logistics, and resource utilization (water, coolant, electricity, etc.) It can also throw light on important external factors such as temperature, and humidity.
4. Integration of AI with IoT
By combining AI with IoT, we add a vital capability to manufacturing – ACT. AI goes beyond the data visualizations presented by IoT: it practically takes appropriate actions based on the data. Instead of just presenting the facts to humans to enable them to act, AI closes the loop by automatically taking an action.
It essentially becomes the brain of the connected systems. By applying deep learning models based on neural networks to incoming sensor data, IoT systems will be able to find anomalies in real-time. When a critical error is predicted by the neural network, the faulty device may be shut down to avoid a fatal accident.
The integration of AI with IoT harnesses the power of predictive maintenance which will help organizations save millions of dollars in support and maintenance of equipment.
5. Lean processes
In mature organizations, processes are based on lean principles. Digital technologies assist in the design and achievement of optimal objectives as standardized work is widely used and site processes are fully integrated.
Key partners and customers are fully integrated and synchronized into site operations through joint strategic projects and standardized processes. In a mature factory, repetitive and high-volume tasks will be completed using robotic process automation (RPA).

6. Technology
Cutting-edge technologies represent a core enterprise attribute of all digitally mature manufacturing companies.
The use of advanced automation, predictive analytics, and disruptive technologies set new digital transformation service standards in manufacturing.
Enterprise systems and technologies, such as operational technology, digital twins, blockchain technology, AI, and machine learning, to name but a few, are part of a fully integrated digital ecosystem involving multitier external partners.
Integration with the manufacturing execution system (MES) is leveraged to improve line-set up-timing, throughput analysis, and production control. Similarly, integration with quality control systems is used to drive better quality control.
In a nutshell
New technologies are completely reinventing the global manufacturing industry. Organizations that gear their enterprises around digital capability will lead and thrive.
Ready to boost your Digital Maturity? Talk to our experts, and find out how we can support your transition to smart manufacturing.
