How to Effectively Reduce Manufacturing Waste Using Data
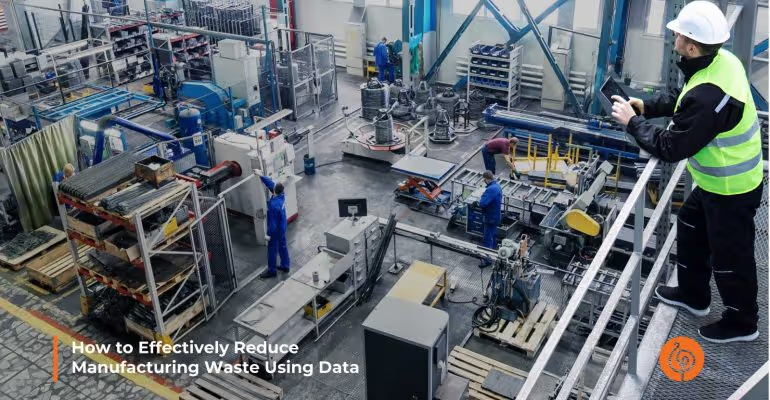
Identifying waste
First and foremost step to reduce manufacturing waste is identifying it. A common problem with most manufacturing companies is that they fail to educate their staff/managers to identify the waste and how it can be reduced. Training the managers, staff with new and advanced technologies and programs can help your manufacturing company reduce waste and improve quality.
Let’s classify different types of waste
Defect waste
Defective documents, machines, quality standards can hurt your manufacturing process significantly contributing to higher expenses. Poor understanding of customer requirements, unplanned downtime, frequent machine repairs, inaccurate data, and human errors can contribute to defects and impact the business bottom-line. These defects will impact the resources used in the entire process and lead to poor outcomes.
Over-processing waste
The slow approval process, lack of communication, data inaccuracy/duplication, human errors can lead to over-processing and this impacts the overall workflow. A poor workflow and process standards could only ruin the production process and quality product development. Standardizing the process is a must to improve the overall workflow and customer experience.
Overproduction waste
Producing products than what is planned is also a waste and overdoing the production can cost the company relatively higher. The excess WIP, product and people movement, siloed operations, poor scheduling can lead to additional scrap and costs heavily. Unreliable processes, inconsistent production schedules, semi or no automation can often lead to overproduction. This type of waste is quite common in most manufacturing companies.
Inventory waste
Inventory consists of raw materials, WIP, and finished goods. Over purchasing, manufacturing or transportation can often lead to inventory waste and this could arm and leg for manufacturers if poorly managed. Lack of demand forecasting, process optimization, and over transportation can lead to this type of waste, and controlling this is extremely critical to improve product development and delivery.
Machine waste
Overproduction or inefficiency leads to machine waste. Using the same machine for long working hours could impact its efficiency. Heat and friction can contribute to machine inefficiencies and lead to machine repairs. Poorly managed and maintained machines could lead to poor productions and costs higher. It’s always important to maintain the machines well to avoid machine repair and labor costs.
Well, by now you’d developed some insights into manufacturing waste and its impact. Let’s dive deep into the discussion of how data analytics could reduce waste and improve process, production, and quality.
Tips to reduce waste using technologies and data analytics
Before getting into data analytics, there comes the significant part of collecting data to use the analytics. When it comes to collecting data and processing it, as a manufacturer you have to focus on the top technologies like the Internet of things, AI, Cloud, Mobile, and Web applications. When all these technologies are used together, garnering data, processing, and analyzing for improvement is extremely seamless and impactful.
All of this is possible using digital transformation services. Let’s see how this powerful combination works.
Efficient defect management
As this type of waste is mostly due to poor data management, lack of standardization and other process flows, streamlining the process with the combination of IoT and mobile applications, the overall process becomes transparent and streamlined.
IoT devices are used in machines to garner data which is pushed to mobile applications of the staff. The staff can push the data to their respective managers or supervisors for adjustments. This saves a lot of time and money. This also avoids approval delays as the entire process is visible to everyone.
Accurate data collection and processing could easily help the manufacturers to foresee the defects in the process and plan for improvements.
Efficient Inventory Management
We saw that inventory comprises raw materials, WIP, and finished goods. Managing the inventory efficiently is important to reduce waste. IoT is a wonderful addition to the manufacturing process to ensure the planned vs. actual production and audit the purchase and dispatch history of products in real-time. This provides complete visibility to the entire inventory process leading to less cost and improved delivery. With the data at the fingertips, it is never difficult to manage the inventory better.
Label and organize the warehouse properly using data analytics to simplify the inventory woes and cost. Identifying products within the warehouse and dispatching them to customers is often troublesome for customers and poor process management leads to increased costs and below-par customer experience. With IoT, RFID, or QR code technology, labeling and organizing the products in the warehouse becomes super easy and makes it easily accessible for staff. By this way, you’d save a lot of time and money.
Smart Predictive Maintenance System
Growing machine repair and labor costs cause headaches to most manufacturers. Inefficient machines and frequent downtimes could only impact the production quality and delivery. With an IoT and AI-based predictive maintenance system, considerable amounts of data can be derived from the machines’ performances and flaws. The data then can be processed and studied to forecast machine faults and failures. With such a system in place, reducing the machine repair and labor costs can be reduced as the entire machine maintenance schedule is streamlined and monitored perfectly.
Conclusion
Leverage technology to reduce manufacturing waste. Considering an industry like manufacturing which deals with lots of processes, resources, and machines, managing waste effectively is critical for ensuring a seamless customer experience through uncompromised product quality. Get started with manufacturing waste management best practices today before your competitor does.
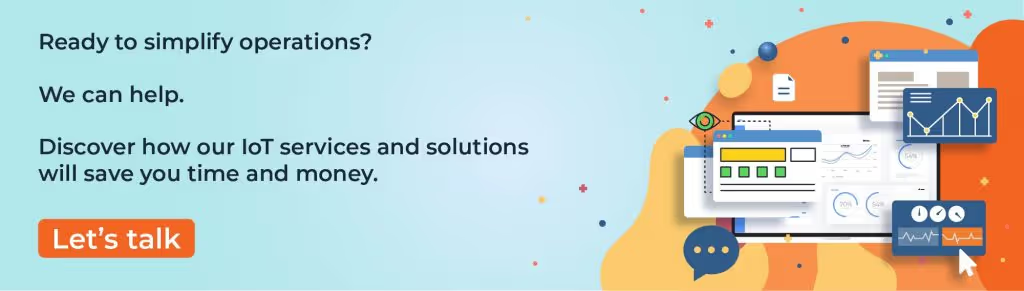