5 Trends Making Connected Workers a Must for Future Manufacturing
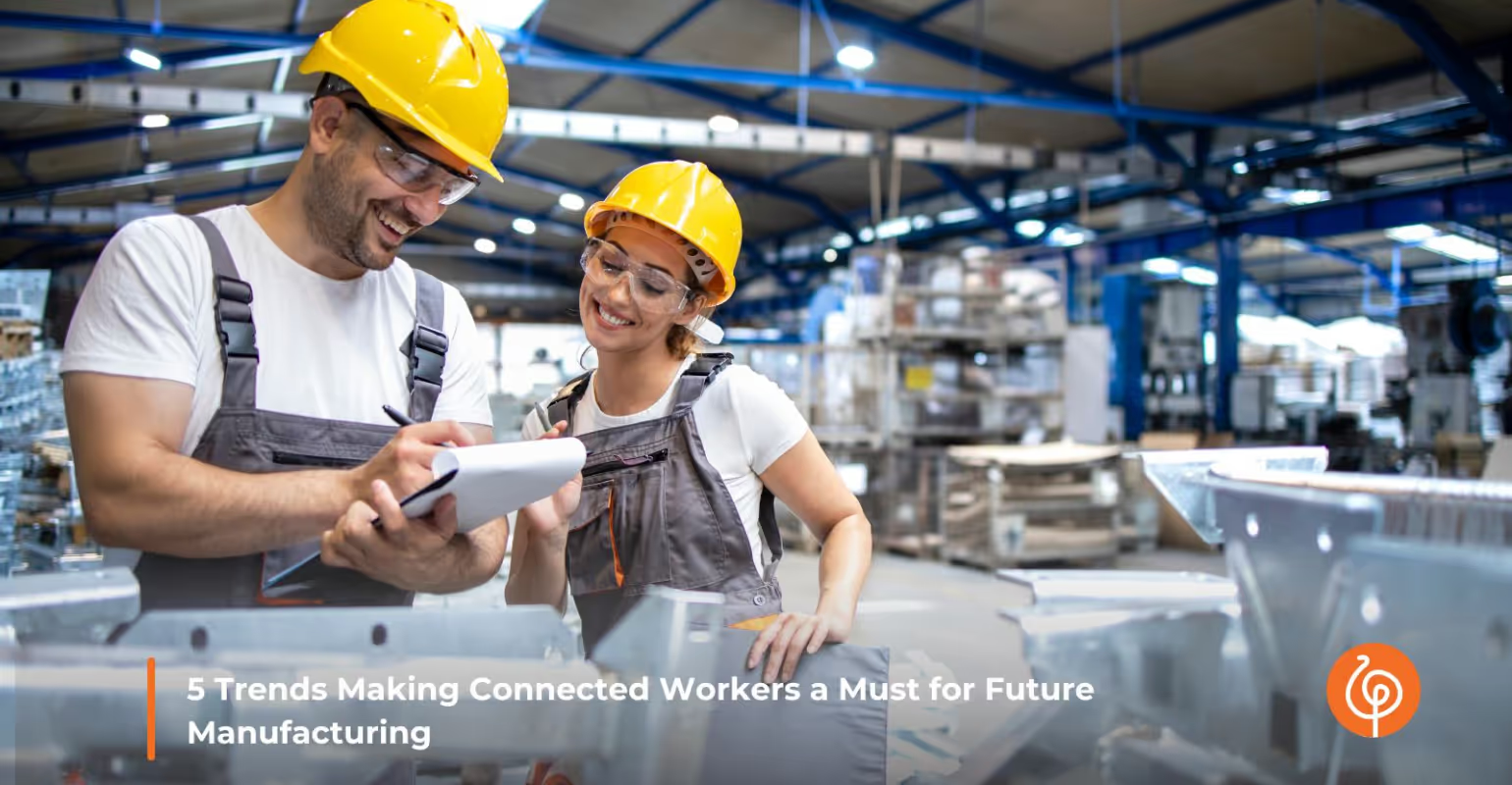
What is wrong with today’s frontline workers’ operations
Most of them rely on manual processes, instructions and task allocations from the supervisors. Delayed processes often lead to below-standard production and impact the morale and performance of the frontline workers.
Safety concerns are widely cited by many workers working in hazardous zones. On the other hand, management has no insights into how the workers operate and how to improve productivity concerning growing demands.
All of the above, garnering real-time data from machines and humans is a challenge for many manufacturers today.
All the above-stated challenges are impacting the overall performance and efficiency of the manufacturing platforms, resulting in below-par production and customer satisfaction.
Industry leaders’ take on negating the present challenges
The leading manufacturers have realized the significance of reinventing how their frontline workers operate and are revisiting the current strategy with a futuristic one. Many have discovered that connected worker platforms will be the future of manufacturing due to the plethora of benefits these platforms offer manufacturers.
They are interested in picking up the latest trends for connected worker solution for manufacturing and their future.
Before getting started with the trends, let’s throw some light on the connected worker platform and why manufacturers should invest in one.
What is a connected worker platform
A connected worker platform is exclusively designed to renovate the way frontline workers operate on a daily basis.
While the platform’s core benefit is improving workforce performance, it also helps everyone in the process with real-time data to achieve improved efficiency.
The management team can also make better decisions with the help of the data obtained using the platform. So, a connected worker platform will completely modify how a manufacturing product floor functions.
How it works
On top of all benefits, the advanced platform helps the frontline workers to connect, interact and share data with everyone in the platform via digital means and on the go.
With the platform, the workers can save a lot of time and some money, as they don’t have to rely on paper-based processes, which cost manufacturing massively.
Also, the technologies used in the platform help the workers to ensure safety while working in hazardous zones. This encourages the workers to perform without any discomfort and quickly.
Here is how the platform works.
The platform is power packed with advanced technologies like the Internet of Things, Artificial Intelligence, Cloud, Enterprise Mobile Applications, etc.
Generally, there are 3 things workers need during production.
- Data collection – Internet of Things technology used in the platform takes care of this part. With the help of IoT devices, garnering data from any interface is breezy.
- Data sharing – Next, the collected data has to be shared with peers or management. Mobile applications in the platform enable workers to share data in real-time instantly.
- Communication from anywhere, at any time – the complete data set is stored in the Cloud available in the platform. Using Cloud technology, workers can access data from anywhere, anytime.
Here is another exciting benefit for the management team. Artificial intelligence in the platform helps the management team make informed decisions for improving production rate and efficiency.
Now, it’s time to focus on the future trends of the connected worker platform. Let’s wait no further and get started immediately.
READ MORE : Connected Workforce Improves Workforce Performance & Productivity
5 Connected worker trends for future manufacturing
1. 5G Edge
Recent developments in the mobile space, 5G, will reinvent the way almost every company operates, and manufacturing is not an exception to this. With 5G-enabled applications, workers can access data from different Cloud models effectively.
2. Automation is the new normal
Manufacturers must say goodbye to paper-based processes. The growth of technologies like IoT, AI, Cloud, etc., clearly indicates that automation is the way to go forward, and only companies that invest in these ever-growing technologies will thrive in the future.
3. AR and VR will be game changers
Augmented Reality and Virtual Reality are already transforming the user experiences for different industry verticals. Though the technology isn’t widely implemented across the manufacturing vertical, its role will be crucial in the near future.
Many companies believe these technologies will help them train their workforce better and save lots of money on onboarding and development programs. The technology-enabled applications can also help the workers to stay from hazardous objects and machines on the premises.
4. Eliminating skill gaps with technology
Labor shortages and skill gaps are considered to be the top most challenge for most companies. With the help of technologies AI and RPA, it is relatively easier to hire candidates with the best skills. In other words, the performance of employees can skyrocket with the help of technical assistance. Technology will also play a role in training the internal workforce whenever needed.
5. Save operational costs and eliminate waste
In the future, avoiding the unnecessary operational cost and eliminating waste is critical for rapid growth and improved RoI. Technologies play a massive part in this. Especially, AI and IoT are used to collect and analyze data from the workforce to readjust the process and workflows to ensure zero wastage and minimal operational costs.
Are your frontline workers highly productive?
Now, it’s time to analyze the performance of your frontline workers.
Have you provided them with the best possible solutions to improve their performance and efficiency? Still relying on manual and paper-based processes?
If your answer is YES to the above, then it’s high time you consider a connected worker platform for your manufacturing plant. Many companies have already started to realize the plethora of benefits offered by the platform.
Be there before your competitor does.
Want to know more about the platform? Want to see how it works?
We’re all ears. Give us a call. Our experts will provide you with all the information you wish to know.
It’s now or never. Want to get started?
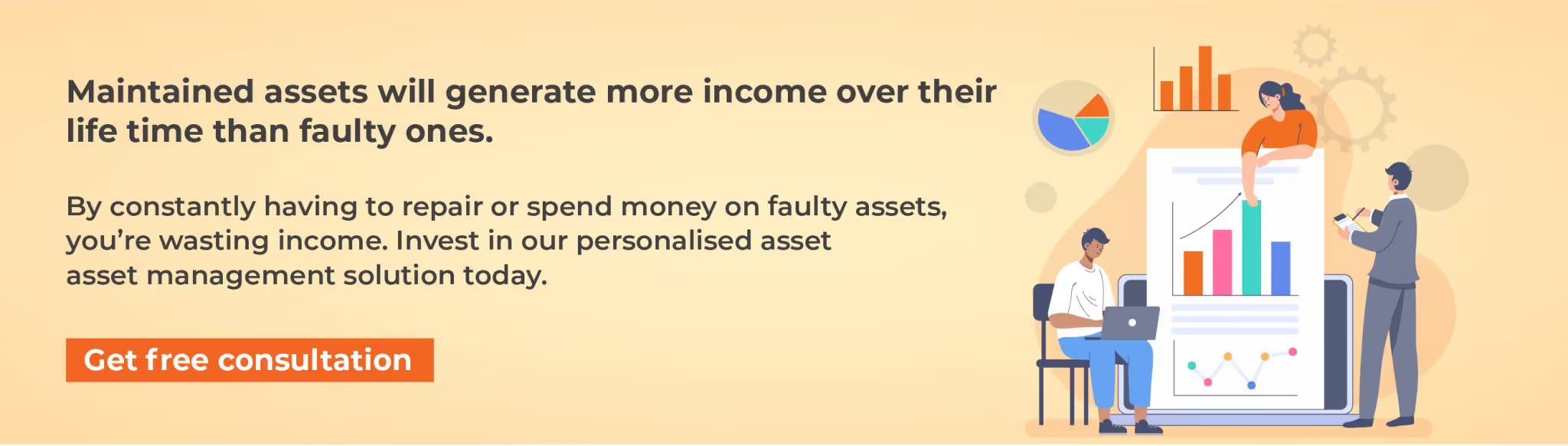