5 Types of Maintenance to Skyrocket Reliability and Performance
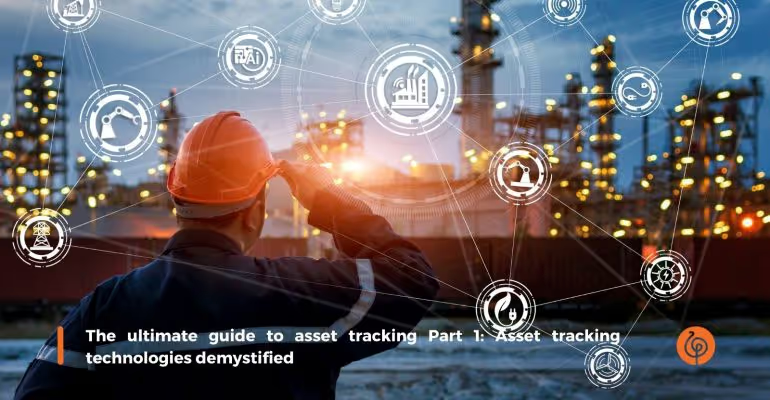
1. Corrective Maintenance
Corrective maintenance is carried out to correct deterioration and malfunctions of any equipment or production line as soon as they occur. To put it simply, you react to whatever happens. It’s a no-brainer, right?
Typically carried out by industrial maintenance technicians, the applied corrective measures simply focus on fixing the piece of equipment and quickly restoring it to a natural working state. This type of intervention can be quite costly for companies, depending on the urgency and extent of the problem.
To put it in perspective, a deep fryer in a commercial kitchen breaks down. Agitated customers are forced to wait while rubbing their hungry bellies. Chefs lose pay and the company’s reputation is damaged with a storm of negative reviews on social media. The staff members watch anxiously, as Fix-It-Felix works hard to repair the fryer.
The silver lining is that corrective maintenance is relatively quick, resulting in brief downtimes and the associated cost is quite low. This type of maintenance is well-suited to restaurants and retail organizations.
2. Preventive Maintenance
Preventive Maintenance is a proactive strategy that involves taking precautionary actions to prevent equipment failures before they actually occur. It usually encompasses frequent inspections, upgrades, lubrication, adjustments, and replacement of outdated components or equipment.
Assigning an oil-change task to a driver after every 1000 miles traveled by a fleet vehicle, changing water filters every 3 months, and cleaning HVAC (heating, ventilation, and air-conditioning) elements at regular intervals are all examples of preventive maintenance.
Preventive Maintenance Solution can help you reduce unexpected equipment failures, increase the lifespan of critical assets, save costs and enhance energy savings. However, it is a labor and time-intensive process which means that you will spend more time and money on inspections in the short term.
It can work well for machinery that is used on a regular schedule, has affordable parts which can be easily replaced, and has a predictable wear-and-tear rate.
Case study: Preventive Maintenance Solution for Manufacturing Company
3. Predictive Maintenance
Predictive maintenance employs advanced technologies such as artificial intelligence, and IoT to predict failures before they actually occur with mindboggling accuracy. Data is collected from assets equipped with IoT sensors and analyzed using machine learning algorithms to identify patterns and predict failure.
The biggest benefit of Predictive Maintenance is that it allows for maintenance to be performed only when absolutely necessary. This directly translates to less money spent on maintenance for a machine that doesn’t actually require it, a massive spike in ROI, and a significant reduction in downtime.
However, IoT sensors do not function optimally in hostile manufacturing environments. In such cases, sensor recalibration and replacement can be quite expensive. Industries that have mission-critical equipment with predictable failure modes, such as food production, oil and gas, manufacturing, and energy plants are ideal candidates for Predictive Maintenance.
To read more: Things you should know about IIoT & Predictive maintenance
4. Conditional Maintenance
Many machines produce some sort of warning of impending malfunction before total breakdown occurs. Condition-based maintenance involves spontaneous action on such machines, which are in the early stages of equipment failure.
Since condition-based maintenance replaces parts when they are expected to fail, manufacturers get more bang for their buck without the damage and downtime that comes from pushing parts to failure as is the case with corrective maintenance.
This type of maintenance involved additional costs associated with frequent monitoring, whether that is done through a sensor or a human inspector. However, these costs are generally offset with savings from reduced downtime as well as part and machine longevity.
This type of maintenance is well-suited to machines that can be easily monitored, require frequent component replacements, and are simple to fix.
5. Predetermined Maintenance
Predetermined maintenance, probably the least popular of all the maintenance types presented in this blog, doesn’t rely on the actual equipment’s state but rather on the programs delivered by manufacturers. They elaborate these programs based on their knowledge of failure mechanisms as well as MTTF (mean time to failure) statistics which they observed on a piece of equipment and its various components in the past.
Maintenance teams have no choice but to rely on these programs so they might not be able to anticipate failures, which means an increased risk of downtime and reduced efficiency. Predetermined maintenance might also involve unnecessary replacement of components, leading to additional costs.

In a nutshell
A mature maintenance program involves a holistic combination of multiple strategies and allows manufacturers to predict component failure with unimaginable accuracy. It also enables them to extend the lifespan of equipment and reduce unplanned downtime.
If you’re looking to get the most out of your maintenance, look no further. With 16+ years of experience in IoT app development, Hakuna Matata is a trusted partner in all things IoT.
We build end-to-end industrial 4.0 solutions using world-class platforms like Microsoft Azure IOT hub and PTC ThingWorx. Our IIOT infrastructure consists of 5 layers, which include existing hardware and software systems, IT- OT integration, data analytics, integration with 3rd party systems (like ERP, HRMS, etc.), and an application layer to help you write your own apps.
Our scalable IIoT infrastructure will empower you with a clear understanding of the overall real-time utilization and behavior of your equipment, irrespective of your location. Our solution is designed to reduce operational costs and boost productivity.
Ready to optimize maintenance? Talk to our experts today!
