How to Increase Machines RoI with Predictive Maintenance
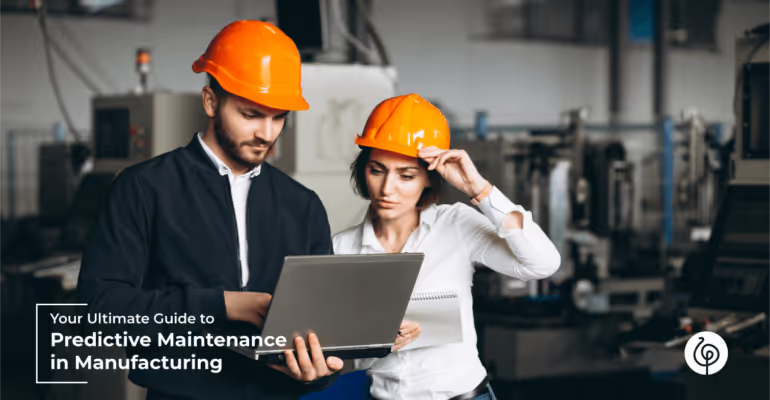
How good is your manufacturing RoI – better, low or high? If it is better or low, you must find out the reasons and fix them at the earliest to achieve high RoI. Of the different factors that contribute to low manufacturing RoI, increasing asset failure and repair costs associated with frequent machine downtimes top the list, in addition to failing to capitalize on the benefits of partnering with a top digital transformation services or IoT app development company.
Common reasons that contribute to machine downtime are
- Ambiguous Working Instructions
- Improper Manufacturing Equipment Maintenance
- Human Error
- Lack of Gathering Downtime Feedback
- Changeovers
- Cleaning
- Tool changes
- Early shutdowns
- Personal breaks
- Excessive machine set-up time
- Unplanned machine maintenance
- On-machine press checks
- Machine operator errors
Here are some of the setbacks manufacturing industries will face due to unplanned downtime.
- Overall equipment effectiveness (OEE) – Availability, performance and quality
- Increasing repair cost
- Delayed production
All of the above factors contribute to increased TCO and reduced value. This is the reason why top manufacturing heads have started to embrace predictive maintenance systems to improve OEE and reduce overhead maintenance costs and production delays.
What is predictive maintenance
In general, the predictive maintenance systems help manufacturing companies with condition-monitoring tools to track the performance of any equipment/machine in idle, normal and peak performances. The data garnered from machines operating at different conditions will help manufacturers plan for maintenance in the near future to prevent sudden failure or downtime.
How predictive maintenance works in manufacturing
Condition-based monitoring is all about collecting real-time data from machines and performing this manual is extremely hard for many humans. With an IoT device and sensors attached to a machine, garnering the real-time data for every single movement of the machine is seamless.
Here are some of the critical parameters captured in real-time by sensors.
- Vibration
- Temperature
- Pressure
- Chemical content
- Liquid/solid levels
The data collected will be pushed to a Cloud from where it is fed into an AI/ML-enabled system to analyze and process data for predicting the future maintenance problems that could arise from that machine. The data processed will be pushed to a maintenance specialist to make plans to negotiate downtime problems.
Benefits of using predictive maintenance for manufacturing
- Capture condition-based real-time data collection accurately
- Foresee & predict machine downtime early
- Higher transparency
- Reduced product delays
- Improved planned production rate
- Lower maintenance costs
- Minimize machine failures
- Reduced downtime for repairs
- Increased machine efficiency
- Improved operator safety
- Verify machine’s performance post-maintenance
- Increased overall profits
According to an Aberdeen report, the average cost of unplanned machine downtime is $260,000 per hour. No wonder such a huge volume of money spent on machine repair impacting the production and profit of any manufacturing company.
Is preventive maintenance not good enough? Yes, say experts. Till date, shop floor plant managers and operators perform planned maintenance and repair machines at regular intervals to prevent downtime. However, these activities are ineffective most of the time.
What is the solution to the persistent problem?
Simply put, preventing machine failures and identifying the patterns that contribute to downtime is critical to driving maximum productivity in the shop floor and reducing overall TCO with respect to machine maintenance. And, this is what predictive maintenance for industry 4.0 is all about.
What is predictive maintenance for manufacturing?
Mostly predictive maintenance analytics are used in shop floors for Machine Monitoring where humans can’t intervene and monitor data.
There are a lot of potential use cases for predictive maintenance. I have highlighted a few for the reader’s reference.
How Industry IoT solutions like predictive maintenance work in manufacturing
Condition-based monitoring is all about collecting real-time data from machines and performing this manual is extremely hard for many humans. With an enterprise IoT solution used in machines, garnering the real-time data for every single movement of the machine is seamless.
- Chemical Industry
Chemical plants collect plenty of data on equipment performance & reliability. And their maintenance process is very rigorous with detailed record-keeping which creates huge data which could be used by Machine learning. The industry can achieve success through digital reliability solutions. For example Improved Condition monitoring of machines through deploying a set of sensors. Even detecting an imminent breakdown a few hours before they occur can help in reducing the time to repair by half and reduce the cost impact by thousands of dollars.
- Tyre Manufacturing
Tyre manufacturing has become more complex than ever due to the increasing number of cars and new modes like electrical & autonomous vehicles. The tyre manufacturing process starts with Mixing & Cooling and goes through various stages like Extrusion, Cutting, Tyre Building, Curing and Labelling. The entire manufacturing process requires process stability and energy efficiency. A most critical component is media (Air, hot water, steam or nitrogen) supply, any interruption would stop entire operations. Predictive maintenance as part of a fully automated solution would certainly help tyre manufactures to conquer the challenge.
- Pipe Manufacturing
Pipe manufacturing is a highly competitive market. Injection moulding and extrusion processes are critical steps of the manufacturing process. Temperature and Pressure play critical roles in defect-free production and has to be monitored continuously. With sensor-based detection/PLC integration, a Predictive maintenance solution can help the pipe manufacturers to proactively monitor and predict the issues which will help in achieving defect-free production.
The manufacturing industry has started to leverage the power of IoT-powered predictive analytics and companies that have successfully implemented such systems are seeing improving productivity and RoI. Looking for IoT solution providers in India? We are experts. Let’s talk.