How to Increase Machines RoI with Predictive Maintenance
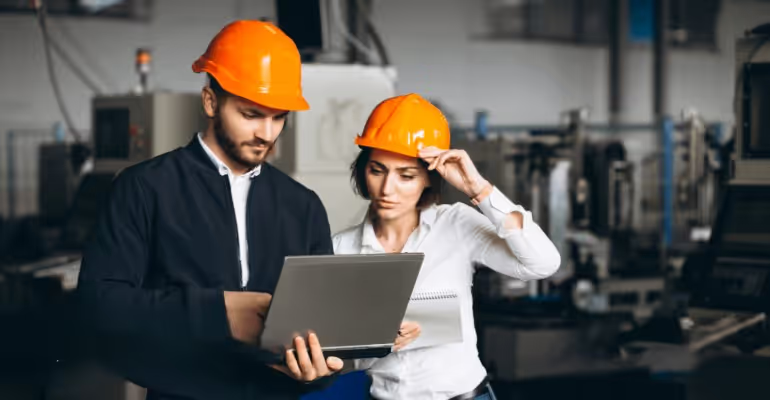
Predictive Maintenance ROI for Enterprise Leaders
As an IoT developer with years of hands-on experience, Iβve seen predictive maintenance ROI revolutionize operations for enterprises in IT, manufacturing, and high-value sectors.
This comprehensive guide dives deep into how predictive maintenance ROI delivers measurable financial returns, minimizes downtime, and positions your organization for long-term success, especially in areas like predictive maintenance in tube manufacturing and IT infrastructure.
Whether youβre a CEO, CTO, or decision-maker in a profit-driven industry, this blog is your definitive resource for understanding and implementing predictive maintenance to achieve predictive analytics maintenance ROI.
From practical steps to real-world case studies, weβll cover everything you need to know in simple, actionable terms.
Table of Contents
- Understanding Predictive Maintenance ROI
- Key Benefits of Predictive Maintenance ROI
- Real-World Applications of Predictive Maintenance ROI
- Step-by-Step Guide to Implementing Predictive Maintenance ROI
- Overcoming Predictive Maintenance ROI Challenges
- Pitching Predictive Maintenance ROI to Stakeholders
- The Future of Predictive Maintenance ROI
- Your Roadmap to Predictive Maintenance ROI Success
What Exactly is Predictive Maintenance ROI? (And Why Should You Care?)
You know how sometimes your car makes a weird noise, and you wish you knew if it was serious or if you had time to get it checked out? Predictive maintenance is like that, but for your industrial machines, servers, or any critical asset.
So, what is Predictive Maintenance ROI?
βSimply put, Predictive Maintenance ROI is the financial gain you get from using smart tech β think IoT sensors, Artificial Intelligence (AI), and advanced data analytics β to predict when your equipment is about to fail, so you can fix it before it breaks down. It's about optimizing your maintenance ROI.
How does it actually work?
βImagine tiny, tireless guardians constantly watching your machines. These are IoT sensors, diligently monitoring crucial metrics like vibration, temperature, pressure, or even power consumption. This data flows into an AI system, which acts like a super-smart detective. It crunches the numbers, looks for subtle patterns that humans would miss, and flags potential issues before they become major problems. This allows your team to intervene precisely when needed, rather than waiting for a catastrophic failure.
Why does this matter for my enterprise?
βBecause unexpected downtime is a profit killer, plain and simple. Deloitte estimates that unplanned downtime costs industries $50 billion annually. That's a huge chunk of change that could be going back into your business.
PdM directly tackles this, bringing a triple threat of benefits:
- Massive Cost Reduction: Less downtime means less lost production, fewer rushed emergency repairs (which are always more expensive!), and smarter inventory management.
- Efficiency on Steroids: Your operations run smoother, consistently, and without those jarring interruptions. This is crucial whether you're running a high-volume tube manufacturing line or trying to guarantee 99.99% uptime for your IT services.
- Strategic Superpower: Leveraging data to make proactive decisions isn't just about saving money; it positions you as an innovative leader. Siemens, a true industrial powerhouse, highlights how this data-driven approach provides a significant competitive edge. Plus, reliable systems build customer trust β especially vital in our always-on IT world.
How is this different from what we're doing now?
βGood question! Most companies are probably doing one of two things:
- Reactive Maintenance (The Firefighter Approach): This is when something breaks, and then you scramble to fix it. Think of it like waiting for your car to die on the highway before calling a tow truck. It's expensive, disruptive, and often happens at the worst possible time.
- Preventive Maintenance (The Calendar Approach): This is scheduling maintenance based on time or usage, regardless of actual need β like changing your car's oil every 3,000 miles, even if you only drove 500. It's better than reactive, but it can waste resources on unnecessary upkeep.
Predictive Maintenance (The Smart Approach): This is the sweet spot. We use real-time data to act only when necessary. It's like your car telling you, "Hey, your brakes are getting worn, but you've got about 1,000 miles left before they become an issue. Schedule a service next week." This targeted approach maximizes your ROI on manufacturing equipment and any other assets.
In fact, Sensemore.io data suggests that predictive maintenance can slash maintenance costs by 20-50% compared to purely reactive methods.
That's a huge potential saving!
So, What's the Big Deal? Key Benefits of PdM ROI
Beyond the high-level concepts, let's get into the nitty-gritty of how predictive maintenance ROI truly transforms your enterprise.
It's about solving real pain points with real data.
Cutting Downtime: How PdM Keeps You Running
Is downtime really that expensive?
βAbsolutely. It's astonishingly costly. The numbers vary by industry, but for a typical manufacturing plant, Sensemore.io estimates downtime can cost upwards of $5,000 per hour.
Think about how quickly that adds up!
How does PdM stop this?
βMy experience, alongside industry reports, shows that implementing PdM can cut unplanned downtime by a staggering 30-50%. How? Those IoT sensors are continuously tracking critical machine metrics. When the AI detects even the slightest deviation that signals a potential failure, it triggers an alert. Your maintenance team gets a heads-up, allowing them to schedule repairs during off-peak hours or planned shutdowns.
Can you give me an example of the savings?
βLet's say a medium-sized factory, currently experiencing 40 hours of unplanned downtime a month (which is pretty common), reduces that by just 20 hours. At $5,000/hour, that's an annual saving of $1.2 million! This directly impacts your predictive analytics maintenance ROI.
Real-Life Scenario (from my work): I recently worked with a client in the food processing industry. They had an aging conveyor system that was notorious for unexpected belt failures, leading to product spoilage and production halts. By installing vibration and tension sensors, we built a model that could predict belt degradation days in advance. In the first six months, they avoided three major breakdowns, saving an estimated $150,000 in lost production and emergency repair costs. The maintenance team was thrilled because they could order parts in advance and swap belts during scheduled overnight cleaning shifts.
Making Your Equipment Last Longer (Seriously!)
Doesn't equipment just wear out eventually?
βYes, but you can significantly extend its useful life and defer expensive capital expenditures. Replacing equipment, especially specialized machinery in predictive maintenance in tube manufacturing, is a massive cost.
How does PdM help?
βBy constantly monitoring operating conditions, PdM helps you maintain equipment in optimal health. Think of it like proactive healthcare for your machines. Instead of simply replacing parts on a fixed schedule, you replace them only when needed, based on actual wear and tear. WorkTrek cites how companies are extending the life of assets like wind turbines through precise vibration analysis.
What's the financial impact here?
βYou defer capital expenditures for years. If a critical machine with a $500,000 replacement cost can be kept running effectively for an extra two years, that's half a million dollars you don't have to spend right now, directly improving your equipment ROI. For IT, this means preventing premature server failures, delaying costly hardware upgrades, and getting more mileage out of your existing data centers.
Smarter Spending: Optimizing Resources with PdM
Are we really wasting money on maintenance now?
βStudies, like those by NumberAnalytics, suggest that traditional maintenance approaches can lead to overspending on labor and parts by as much as 30%. That's a lot of inefficiency.
How does PdM fix this?
βBecause PdM schedules maintenance only when it's genuinely needed, you're not paying technicians for unnecessary inspections or replacing parts that still have plenty of life left. Imagine saving $36,000 per year on a $120,000 maintenance budget just by being smarter about when and how you maintain.
Does it integrate with our other systems?
βAbsolutely. Linking your PdM system with your ERP (Enterprise Resource Planning) and CMMS (Computerized Maintenance Management System) is key. As Opsio suggests, this integration optimizes inventory management, ensuring you have the right parts at the right time, without tying up capital in excess stock.
This frees up resources for strategic investments, dramatically enhancing your overall maintenance ROI.
Building a Safer Workplace (It's More Than Just Money)
Is predictive maintenance really a safety tool?
βUndeniably. Equipment failures aren't just about financial loss; they carry significant risks of accidents, injuries, and serious legal liabilities.
How does PdM contribute to safety?
βBy detecting potential issues early, PdM acts as a crucial safety net, preventing catastrophic failures. IIoT World highlights a compelling case of a chemical plant that avoided a major incident, safeguarding both personnel and the environment, through their PdM implementation. In IT, ensuring reliable systems avoids service disruptions that can lead to customer data loss or breaches, preventing significant reputational damage and potential penalties.
The Outcome: A safer environment for your employees, reduced legal and financial risks from incidents, and a stronger company reputation β all contribute to a holistic predictive maintenance ROI.
It's about protecting your people, your assets, and your brand.
Real Talk: Where is Predictive Maintenance ROI Actually Happening?
It's one thing to talk theory; it's another to see it in action. These real-world examples and case studies demonstrate the tangible impact of predictive maintenance ROI across various industries.
Predictive Maintenance in Tube Manufacturing: A Deep Dive
How does PdM apply to something as specific as tube manufacturing?
βIt's highly effective! In tube manufacturing, equipment like extruders, rolling mills, and cutting machines operate under immense stress. Even minor wear can lead to defects, material waste, or worse, a complete line stoppage.
What's the typical application?
βHere, sensors meticulously monitor the vibration of rollers, the temperature of extrusion dies, and the power consumption of motors. AI models analyze these patterns to detect subtle signs of wear or misalignment before they impact product quality or cause a breakdown. Maintenance can then be scheduled during planned downtimes, like shift changes or weekend shutdowns, preventing costly interruptions during peak production.
What kind of results have you seen or heard about?
βA well-known Siemens case study demonstrated a 15% reduction in lifecycle costs for equipment in manufacturing by leveraging PdM. This significantly boosts predictive maintenance ROI manufacturing. One tube manufacturer I know used vibration sensors to pre-emptively detect bearing wear in a critical rolling mill. By replacing the bearings during a scheduled maintenance window, they avoided an estimated $200,000 in annual downtime costs that had plagued them in previous years. It improved product consistency too, as worn bearings often led to uneven tube thickness.
Keeping Your Servers Happy: PdM in Enterprise IT
Predictive maintenance for computers? How does that work?
βAbsolutely! In enterprise IT, "equipment" includes servers, cooling systems, network devices, and storage arrays. An outage in any of these can halt operations, lose data, and alienate customers.
What's being monitored?
βThink about monitoring server temperatures, fan speeds, power supply fluctuations, disk I/O performance, and even network traffic anomalies. AI can detect patterns that indicate an impending hard drive failure, an overloaded server rack, or a failing cooling unit.
What are the benefits in IT?
βLenet reports that companies implementing PdM for their IT infrastructure see a 30-50% reduction in downtime. For example, Philips Healthcare, as highlighted by OpenText Analytics, achieved a remarkable 30% reduction in downtime across their medical imaging systems. They also boosted their first-time fix rates to an impressive 84% because technicians arrived knowing exactly what the problem was.
This directly translates to improved customer trust, compliance, and a strong ROI on manufacturing equipment equivalents in the IT realm.
Imagine the impact on patient care or critical financial transactions!
Powering Up Profits: PdM in the Energy Sector
How is PdM used in something as massive as energy infrastructure?
βIn the energy sector, we're talking about massive assets like wind turbines, power generators, and grid components. A failure here can mean widespread outages and significant financial penalties.
What does it look for?
βSensors detect minute imbalances in turbine blades, abnormal vibrations in generators, or overheating in electrical transformers. This allows for scheduled repairs during periods of low demand or low wind, ensuring consistent energy output.
Any tangible results?
βWorkTrek points to extended turbine life and reduced energy losses. Iβve seen analyses where a large wind farm, by proactively monitoring turbine health, saved an average of $500,000 annually by avoiding unplanned, emergency repairs and optimizing energy generation.
This is a huge contributor to predictive analytics maintenance ROI for utilities.
A Manufacturing Success Story: 250% ROI, No Kidding!
Can you share a real, high-impact case study?
βOne of the most compelling examples comes from a Siemens study where a large manufacturer integrated PdM across several of its critical production lines.
The Outcome: This wasn't just a small win; they achieved a stunning 250% ROI within just 18 months! This came from a combination of drastically reduced downtime and significant labor cost savings. For example, they saw a 40% reduction in emergency maintenance calls and a 15% increase in overall equipment effectiveness (OEE).
My Key Takeaway from such cases: Start small, focus on your most critical assets (those that cost you the most when they fail), and prove the value. Then, and only then, scale. Use real-time dashboards to continuously track those savings β itβs powerful for internal validation and securing future investment. This is the essence of a successful predictive maintenance ROI case study manufacturing.
Ready to Get Started? Your Step-by-Step Guide to PdM ROI
Okay, so you're convinced! Now, how do you actually get this off the ground in your organization?
Hereβs a practical roadmap based on years of implementation experience.
Start Small: The Power of a Pilot Program
Why a pilot? Can't we just go all in?While the vision is enterprise-wide transformation, jumping straight into a massive rollout is risky. A pilot program allows you to test the technology, processes, and team adoption on a smaller scale, proving the value without a huge upfront commitment.
As Prometheus Group suggests, focus on high-value assets.
How do we pick what to pilot?
βChoose an asset that is:
- Critical to your operation: If it goes down, it costs you serious money or causes major disruption.
- Prone to failures: You have a history of unexpected breakdowns.
- Measurable impact: You can clearly track the before-and-after metrics (downtime, repair costs).
Example: A chemical plant I worked with launched a pilot on a single, aging pump that frequently failed, causing production bottlenecks. Their initial investment was around $75,000 for sensors and software licenses. Within 9 months, they avoided two major pump failures, saving an estimated $300,000 in lost production and repair costs.
That's a 4x ROI on their pilot in less than a year, as similar scenarios highlighted by Jarkoindustry show. This success story made it easy to get buy-in for a broader rollout.
Garbage In, Garbage Out: Why Data Quality is King
What's the most important thing for accurate predictions?
βYour data. Plain and simple. If your sensors aren't accurate or your data isn't clean, your AI models will give you "garbage out," leading to false alarms or missed predictions. This completely undermines your predictive maintenance ROI.
How do we ensure good data?
βInvest in high-quality, industrial-grade sensors. Don't skimp here. Also, choose robust data platforms that can handle the volume and velocity of IoT data. Sensemore.io stresses this point because reliable data is the foundation of reliable predictions. My experience taught me that regular sensor calibration (every 6-12 months, depending on environment) is non-negotiable.
Should this connect with our existing systems?
βAbsolutely. Integration with your ERP and CMMS systems is vital. As Opsio advises, this creates a holistic view of your assets, maintenance history, and inventory, making your PdM insights even more powerful.
Get Your Team on Board: Training for Success
Will our maintenance team resist this new tech?
βResistance is common with any new technology. But in my experience, the key to success is getting your team invested. They are the ones on the ground, and their adoption drives PdM's success.
How do we do that?
βHands-on training is critical, as Prometheus Group emphasizes. Don't just show them slides; let them interact with the dashboards, understand how the data is collected, and see how the predictions are made.
My Personal Insight: During an IoT deployment for a large manufacturing client, we built custom, user-friendly live dashboards for the technicians. We spent hours with them, not just showing them what to do, but why it mattered. When they saw how PdM could proactively identify issues, reducing their late-night emergency calls and making their jobs safer and more predictable, they became PdM's biggest advocates.
We even celebrated their "saves" β the breakdowns they prevented!
Embrace the Future: AI and Cloud Are Your Friends
Why AI and the cloud?
βCloud platforms offer incredible scalability and flexibility, allowing your PdM system to grow as your needs expand. And AI is what makes the predictions truly intelligent, constantly learning and improving its accuracy. In fact, SNS Insider data shows cloud-based PdM was dominant in 2023, reflecting its widespread adoption.
What kind of AI are we talking about?
βWe're talking about machine learning algorithms that can sift through years of sensor data, maintenance logs, and even environmental factors to identify subtle correlations that signal impending failure. OpenText Analytics, for example, highlights how AI dramatically enhances fault detection capabilities.
Any tips for choosing vendors?
βLook for vendors who offer scalable, secure cloud solutions. Ask about their AI models, their data privacy policies, and their integration capabilities with your existing infrastructure. This is a long-term partnership, so choose wisely.
Prove It: Measure, Show, and Scale!
How do we know if it's actually working?
βMeasuring your predictive maintenance ROI is crucial for justifying expansion and celebrating success. Don't just assume; track everything!
What metrics should we track?
βKey Performance Indicators (KPIs) include:
- Reduced unplanned downtime (hours/incidents)
- Lower emergency repair costs
- Extended equipment life (years added)
- Optimized spare parts inventory (reduced holding costs)
- Improved maintenance team efficiency (reduced overtime, planned work)
AVEVA reports some companies achieving a remarkable 1:30 ROI within a year!
Then what?
βOnce you've proven the value with your pilot and collected compelling ROI data, you can confidently scale. If it worked wonders on one production line, imagine the impact across an entire facility or multiple plants. Use those KPI dashboards to communicate your success clearly and consistently to all stakeholders. This transparency builds momentum for wider adoption.
Bumps in the Road? Overcoming Predictive Maintenance ROI Challenges
It wouldn't be a real guide if I didn't address the challenges. While the path to PdM ROI is rewarding, it's not without its hurdles.
But don't worry, they're all surmountable with smart planning.
Keeping Your Data Safe: Cybersecurity Concerns
Is collecting all this data a security risk?
βYes, it's a valid concern. Your IoT devices are gathering sensitive operational data, and any breach could be serious. Cybersecurity is paramount.
What's the solution?
βThe answer lies in robust security measures. Implement strong encryption for data in transit and at rest. Choose secure platforms and partner with vendors who prioritize cybersecurity, offering certifications like SOC 2 or ISO 27001. WorkTrek emphasizes this focus on security.
Real-Life Scenario: I know of a large pharmaceutical manufacturer that implemented cloud-based PdM. Their IT team was initially wary about data moving outside their firewalls. We worked closely with their security team, demonstrating the platform's multi-layered encryption, intrusion detection, and regular third-party audits. By using a certified cloud provider, they gained confidence and avoided the potential breaches that could have come from less secure, on-premise solutions.
Old Systems, New Tech: Bridging the Gap
Our older machines and systems aren't exactly "smart." How do we integrate them?
βThis is a common challenge. Many legacy systems weren't built for modern data collection or integration.
What's the trick?
βMiddleware. Think of it as a translator that allows your old systems to "talk" to your new PdM tools. Deloitte advises leveraging these integration layers. Don't try to rip and replace everything at once.
Tip from the Trenches: Pilot your integrations on a single legacy system first. Work out the kinks, understand the data flow, and refine the process before rolling it out widely. An IT firm, for instance, successfully integrated PdM with their aging server monitoring tools, leading to a 40% reduction in downtime for those specific legacy servers. It proved that old dogs can learn new tricks with the right approach.
The Initial Investment: Making the Numbers Work
This sounds great, but I'm worried about the upfront costs.
βIt's true, there's an initial investment in sensors, software, and training. This can be a barrier.
How do we manage this?
βStart with SaaS (Software-as-a-Service) models. As Jarkoindustry points out, these typically have lower upfront costs and a subscription-based payment, making them easier to budget for.
The Bottom Line: Focus on the massive returns. Remind your stakeholders that those $1.2 million per year in downtime savings (or more!) can quickly dwarf the initial investment. A factory I'm familiar with used a $50,000 SaaS pilot and achieved a whopping $500,000 in savings within their first year, demonstrating a clear and compelling ROI. Frame it as an investment in future profitability, not just an expense.
How to Sell This Internally: Pitching Predictive Maintenance ROI to Stakeholders
You've done the research, you understand the benefits, and you're ready to make a move. Now, how do you get your CEO, CFO, and other decision-makers on board? It's all about a compelling, data-driven pitch that addresses their concerns.
Speak Their Language: Data, Data, Data!
What's the most effective way to get their attention?
βNumbers. C-suite executives are driven by financial performance.
How do I use data effectively?
βDon't just say "it saves money." Show them! Cite real results like the 250% ROI from the Siemens case study, or the $36,000 in labor savings reported by NumberAnalytics. If you have internal data from your pilot, that's even better.
My Personal Recommendation: Tailor your data. If youβre talking to someone in predictive maintenance in tube manufacturing, emphasize the cost of production line stoppages. For an IT leader, focus on outage costs and customer churn.
A CTO I advised won approval by presenting a clear spreadsheet detailing $1 million in potential savings over three years, directly tied to PdM implementation.
It wasn't just a vision; it was a financial plan.
Solve Their Problems: Address Their Pain Points
How do I make it relevant to them?
βEvery leader has a unique set of challenges. Frame predictive maintenance as the solution to their biggest headaches.
Examples:
- For a manufacturing plant manager, it's about reducing unexpected downtime and meeting production targets.
- For a CFO, itβs about reducing operational expenses and improving capital asset utilization.
- For a CTO, it's about guaranteeing service uptime and enhancing system reliability (as highlighted by Lenet).
Tip: Before your pitch, do your homework. What are their top three priorities this quarter or year? How does PdM directly help them achieve those? Tailor your message.
Think Big Picture: Show Scalability
How do I make them see the long-term vision?
βLeaders want to know that an investment today can grow into something even more valuable tomorrow.
What to highlight: Discuss how cloud-based and AI-powered PdM solutions offer inherent scalability (as SNS Insider's market growth indicates). Show them how a successful pilot can be replicated across multiple plants, departments, or even globally.
The Strategic Play: Emphasize how PdM isn't just a cost-cutting measure; it's a strategic move that positions your company as a leader, leveraging cutting-edge technology for operational excellence. I've seen manufacturers scale PdM from one plant to an entire global operation, saving over $2 million annually by the third year. That's a story that truly resonates with the C-suite.
What's Next? The Future of Predictive Maintenance ROI
Predictive maintenance isn't a static solution; it's continuously evolving. As an IoT developer, I can tell you that the future holds even greater promise for predictive maintenance ROI.
Cool New Tech on the Horizon
- Edge Computing: Imagine processing data right where it's collected β on the machine itself. This reduces latency, making real-time decisions even faster and more efficient. Think instant alerts and immediate adjustments.
- Digital Twins: These are virtual replicas of your physical assets. You can run simulations on the digital twin to test maintenance scenarios, predict behavior, and optimize performance before touching the real equipment. AVEVA is a big proponent of this for better predictions and asset management.
- Augmented Reality (AR): Picture maintenance technicians wearing AR glasses that overlay digital instructions, diagrams, or even real-time sensor data directly onto the equipment they're working on. This guides repairs, improves accuracy, and boosts efficiency.
- 5G Integration: The rollout of 5G networks is a game-changer. It means faster, more reliable data transfer from thousands of IoT sensors, enabling truly real-time insights and more responsive predictive models.
Market Trends: Why Now is the Time
- Explosive Growth: The predictive maintenance market is booming. SNS Insider projects it will reach a staggering $105.66 billion by 2032! This isn't a niche trend; it's a mainstream industrial revolution.
- Widespread Adoption: Companies in IT, manufacturing, energy, and transportation are rapidly adopting PdM. Early adopters are already gaining a significant competitive edge through reduced costs and improved reliability.
- Sustainability Focus: Beyond the financial benefits, PdM contributes to environmental sustainability. By optimizing equipment performance and extending asset life, it reduces waste, energy consumption, and the need for new equipment manufacturing β aligning perfectly with crucial ESG (Environmental, Social, and Governance) goals.
My Firm Belief: Investing in predictive maintenance now isn't just about catching up; it's about leading the pack. It's about building a resilient, efficient, and profitable enterprise for the decades to come.
Your Roadmap to PdM ROI Success: Let's Do This!
So, there you have it. Predictive maintenance ROI is not a myth; it's a proven, powerful strategy to cut costs, boost efficiency, and future-proof your enterprise. For leaders in IT, predictive maintenance in tube manufacturing, and every other high-value sector, PdM delivers tangible maintenance ROI through intelligent, data-driven decisions.
My advice, built on years of hands-on experience, is to start small, rigorously ensure data quality, truly invest in training and empowering your teams, and then scale strategically.
This approach is how you unlock millions in savings and transform your operations.
Your Next Steps to Turning Downtime into Profits:
- Calculate your current downtime costs: Seriously, put a number to it. This is your baseline and will immediately highlight your biggest PdM opportunities.
- Explore solutions from reputable providers: Look into what companies like Siemens or OpenText are offering in this space. Ask for demos specific to your industry.
- Launch a low-risk pilot on a critical asset: Don't try to boil the ocean. Pick one key machine or system and prove the concept.
- Share this guide with your team: Get everyone aligned and excited about the journey ahead.